Home » 5S Implementations » 5S Audit
5S Audit
In a 5S audit the 5S level of the workplace is assessed. A 5S audit is typically conducted at the end of a 5S implementation. Using a 5S checklist supported by the hands-on 5S App, it is measured whether 5S has been effectively applied within the organization. Here you can read what an audit looks like in practice and the different ways 5S Company uses audits.
- Early identification of problems
- Invest in process improvement and optimization
- Increase safety and job satisfaction
- Reduce waste of time, materials and tools
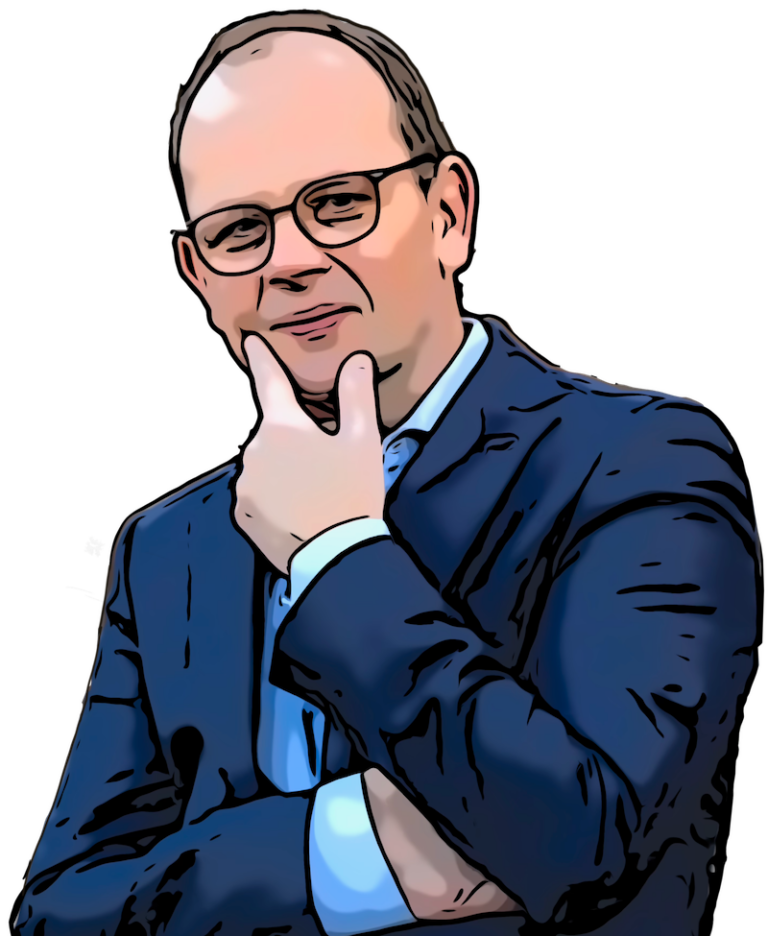
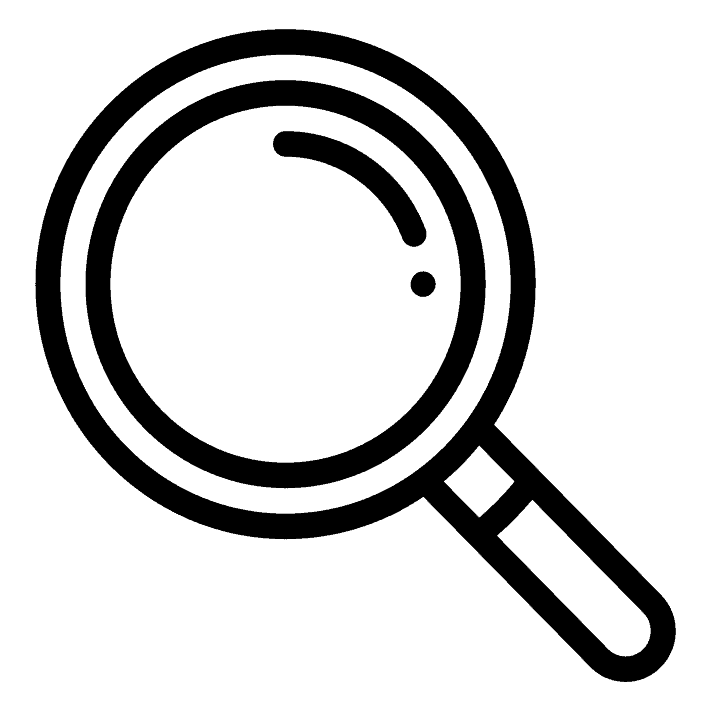
How does a 5S audit work in practice?
Conducting a 5S audit is always done together with a team leader or employee of your organization. The size of the shop floor determines the duration of the audit. In addition, the 5S level Whether the audit is conducted at a pre-planned time or unscheduled.
Lean 5S checklist and 5S audit board
A regular part of the 5S audit is the 5S checklist. In this checklist, all 5 S's of the 5S method checked: separating, cleaning, arranging, standardizing and persevering. The checklist also assesses the 5S level on the basis of scores between 0 and 100 percent. In addition, the checklist itself not only tests the 5S level of the workplace, but also the 5S DNA of the employees.
Although the 5S method has a permanent place in the checklist, situations as they occur in practice are also examined during the audit. The Lean 5S checklist-template is adjusted immediately after the rolling out 5S in the organization to the conditions of the shop floor. Thus, practice forms the basis for arriving at the correct measurements.
During the 5S rollout, all the S's from the 5S model are put into practice. These are the steps of the execution phase of the 5S implementation on your workplace.
5S training is designed to familiarize everyone in a company with the 5S method. Work on effectively implementing 5S within your organization and become a star at 5S!
The initial introduction and analysis of the shop floor. During the Gemba Walk, processes and waste are accurately identified for effective rollout of the 5S method.
The four steps of the 5S audit
1. The 5S audit starts with a check in the 5S App. This shows what outstanding actions there are and whether the actions and areas for improvement have been worked on. Through the 5S App, all situations in the list of work in progress are tracked. Both situations that need improvement and the positive aspects and progress of 5S on the shop floor.
2. The next step is to walk around the shop floor: the Gemba walk. During this round, all 5 S's of the 5S method are checked against a 5S checklist. In addition, the entire workplace is also checked and various employees are interviewed during the inspection round and asked about their experiences, ideas and possible obstacles.
3. After the Gemba walk, the scores for each S are entered into the Lean 5S checklist. From this, the current 5S level of the organization becomes clear and advice is also developed to improve the 5S level of the organization.
4. At the end of the audit, the results are shared with the entire teams. This is often done by means of an extensive semi-digital 5S audit board. Through a 5S board the findings of the round are shared with the employees in an effective manner. By presenting the results of the audit to all employees, employees are directly involved in the result and at the same time necessary actions can be coordinated immediately.
When do you initiate an audit?
The 5S audit is a valuable tool for improving and accelerating effective 5S implementation in the organization. The audit can be used for a variety of purposes.
- 5S Company audit service as training
By conducting the audit together with an employee, a piece is found at the same time 5S training place. This training ensures that the knowledge is in-house to carry out internal audits independently in the long term.
- Understanding current 5S level
A 5S audit provides insight into the current 5S level of the workplace. The checklist assesses the Gemba of that moment "real time. This minimizes the time between obstacle and solution. Points for improvement can be translated directly into tasks within the team, with clear agreements on roles and deadlines.
- 5S assurance
The audit enables an organization to secure 5S. After each audit, the results are recorded in the 5S App stored. These scores provide a clear picture of progress over a period of time and what potential stumbling blocks to 5S are in the workplace. This also allows employees themselves to monitor the 5S level of the work environment.
- Maintaining 5S
“Maintaining” 5S is proving difficult in practice for many companies. The external audits are a big stick to maintain the 5S level already achieved and to strive for progress. To ensure that 5S is not only sufficiently applied at the time of the audit, unplanned audits are therefore carried out by 5S Company as an external party.
5S Company's extensive experience shows that these periodic checks are a welcome help for all industries and all 5S levels. Together with your 5S specialist you can tune in periodic audits even well after 5S implementation to maintain the 5S level of the shop floor.
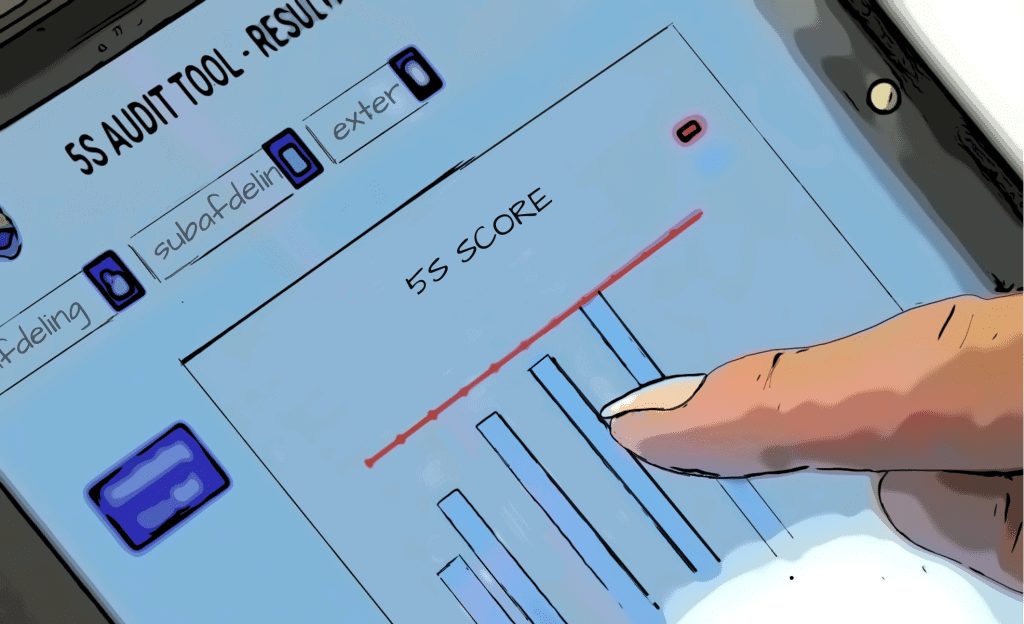
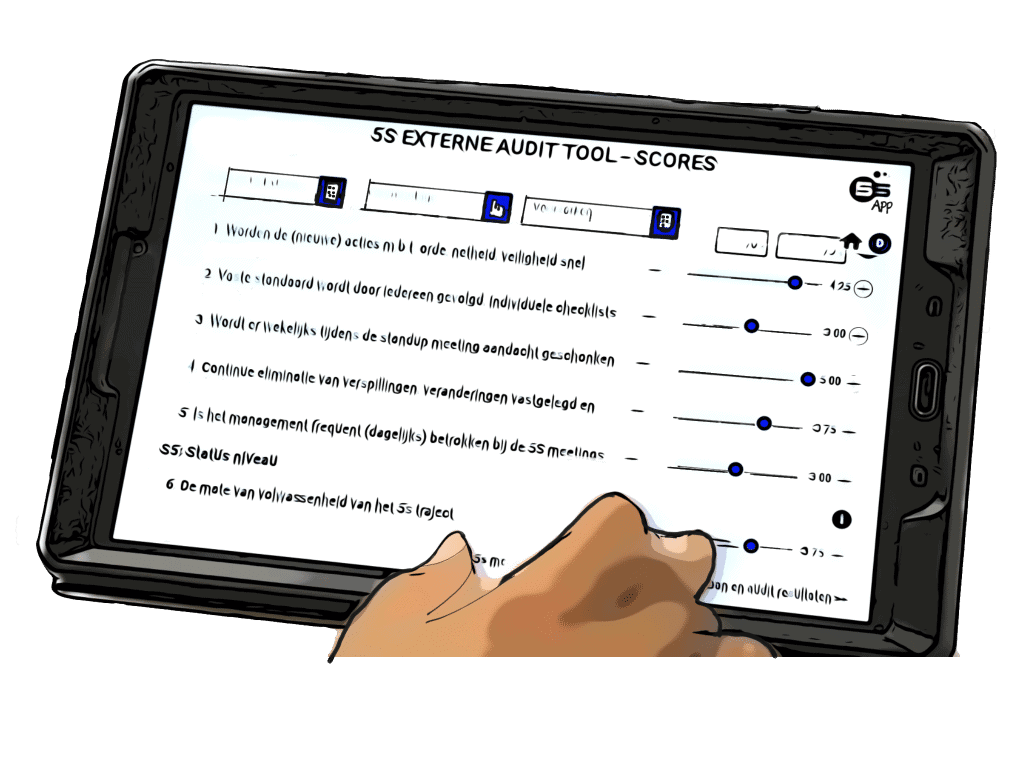
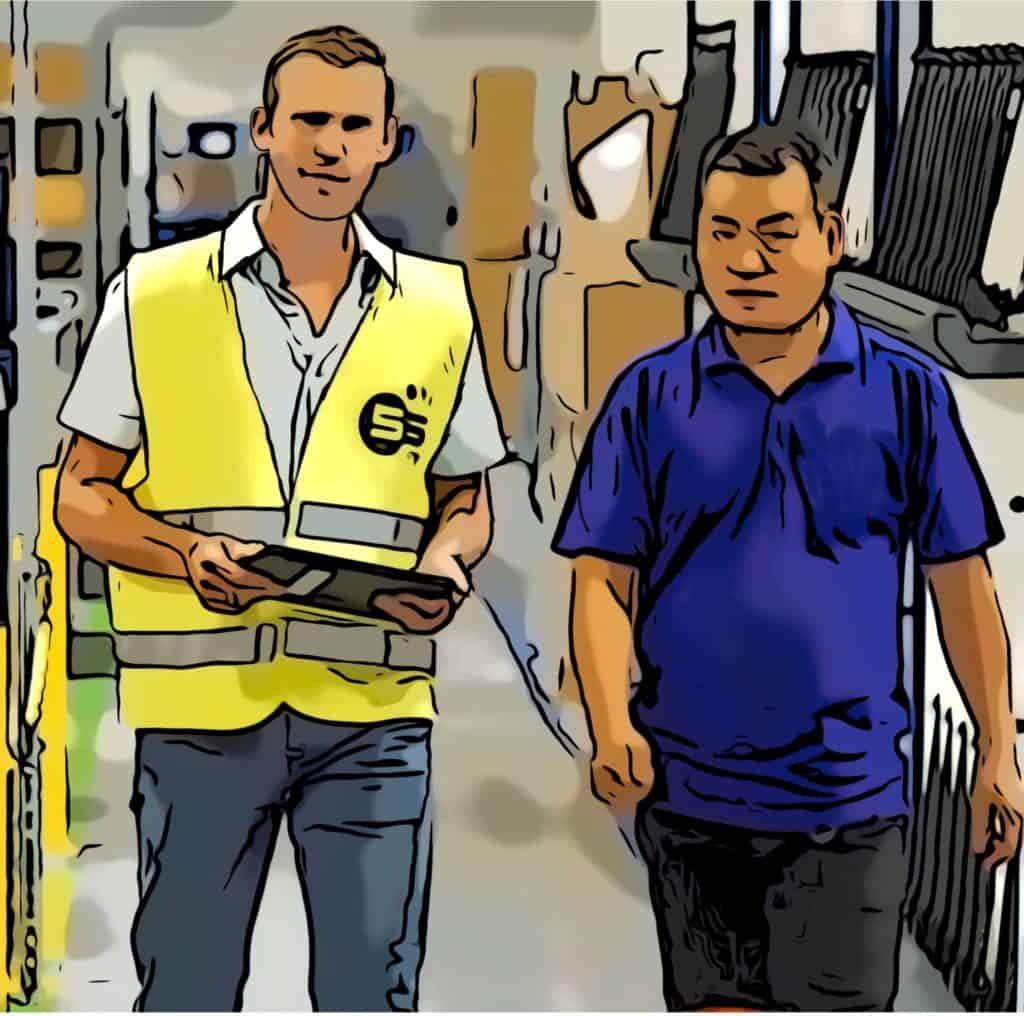
Discover your 5S level now with no obligation!
Are you curious what your current 5S level is? Or would you like to discuss outscourcing 5S audits ? Meet the specialists at 5S Company. Through our Lean 5S audit checklist and 5S App, we can conduct an audit in any industry simply, effectively and quickly. Based on your organization's 5S level, you will receive practical advice and a targeted approach to take the shop floor to the next level. Please feel free to contact us for customized 5S advice.
5S can be applied to any workplace, within any industry. Find out how 5S Company helps you work more safely, efficiently and profitably. A successful 5S implementation in three phases.
Get more insight and control over the results of your 5S deployment with the 5S App. The application supports you in securing 5S on the shop floor and easily conducting 5S audits.
Sort, shine, set in order, standardize and sustain. These are the 5 S's of the 5S Method. Read all about the benefits and application of the 5S Method, 5S Company's specialty.