What is the difference between 5S and 6S?
Are you considering applying 5S or 6S but don't know the difference? Then this article is for you.
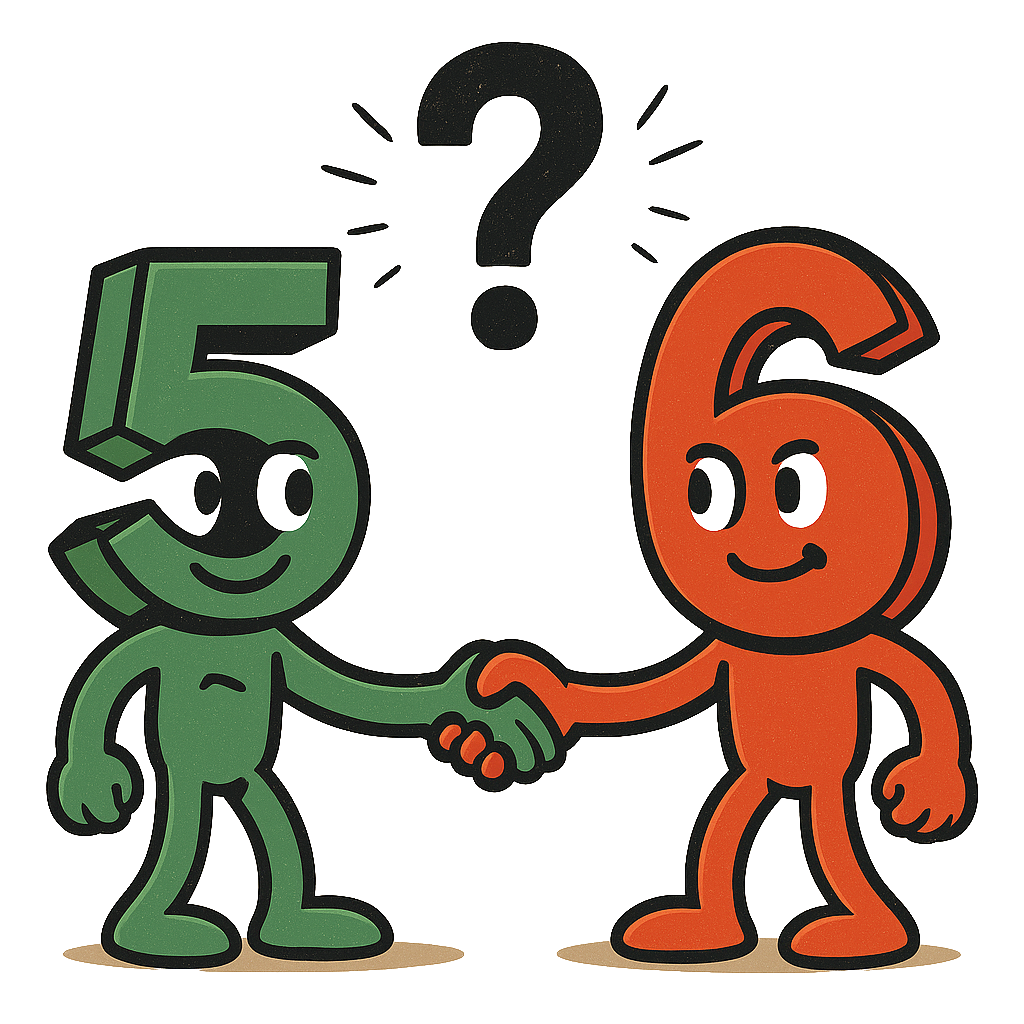
What is 6S - and where did it come from?
Although the 5S methodology became known worldwide by Toyota, its origins actually lie with Henry Ford. As early as 1926, he described in his book Today and Tomorrow the so-called CANDO model:
PDCA = Cleaning up
A = Arranging
N = Neatness
D = Discipline
O = Ongoing improvement
It is very similar to what we now see as 5S know. Toyota, and later Taiichi Ohno in particular, refined these principles into a practical working method within the Toyota Production System (TPS). Thus was born the famous Japanese 5s variant:
- Seiri (Separation) - Remove unnecessary stuff.
- Seiton (Arranging) - Giving everything a permanent place.
- Seiso (Cleaning) - Clean and inspect regularly. (When rolling out, we reverse 2 and 3)
- Seiketsu (Standardize) - Ensure that the first three S's are structurally secured.
- Shitsuke (Stand your ground) - Develop discipline and ownership to keep it up.
In Japan, they once started with only 4S. The fifth S, Shitsuke, is implicitly part of Japanese (work) culture. If you agree on something there, the employee lives up to it. In the West, we had to add it explicitly because discipline and continuous improvement are less obvious here.
Introduction of 6S (5S + Safety)
In the Western world, sometimes a sixth S added: Safety. So with that, 5S becomes "6S. It sounds logical: safety is important - so give it a place in the method. Methodically, little changes, because in a good 5S approach, safety is throughout the structure ingrained. Consider:
- At Sort (Seiri) remove items that pose tripping or fire hazards.
- By Set in Order (Seiton) prevents tools from lying around - so less chance of injury.
- Shine (Seiso) helps detect leaks or wear in time.
- Standardize (Seiketsu) Makes safety checks part of the routine.
- And with Sustain (Shitsuke) keep people alert and engaged - even on unsafe situations (as part of the regular 5s rounds).
- Safety: Ensuring a safe work environment by identifying and managing risks during the initial 5S and
In other words: Safety is in the fabric of 5S. The sixth S (6S) is then a logical consequence, a fundamental result of good 5S policies.
5S and 6S: same method and intention
5S and 6S may seem different, but they ultimately share the same steps and ambition: a safe, structured and efficient workplace. The sixth S is a value fully aligned with the Lean philosophy.
But where 6S names safety explicitly, 5S ensures that safety arises implicitly with each S, if you take the method carefully and with discipline. Safety then is not an extra step, but a direct result of smart organizing.
We therefore put Safety at the center of the 5s circle because each step contributes to it.
What does it provide?
- A safe workplace
- Engaged employees
- Simplicity: standard part of your work
- Sustainable assurance
- In other words, those who take 5S / 6S seriously, builds in safety at the source. This not only makes it more effective, but also much more sustainable.
Conclusion
Those who value safety do not need to add a sixth S right away; they can, of course. Above all, you must get the 5S steps right, then safety follows as a result. With engaged teams, clear standards and continuous workplace maintenance, a safe work environment naturally emerges. That's the essence of Lean - and the power of 5S and 6S.
6S, difference 5S and 6S, lean 5S, workplace safety, 5S safety, Toyota 5S, lean safety, lean management