Was ist der Unterschied zwischen 5S und 6S?
Erwägen Sie die Anwendung von 5S oder 6S, kennen aber den Unterschied nicht? Dann ist dieser Artikel genau das Richtige für Sie.
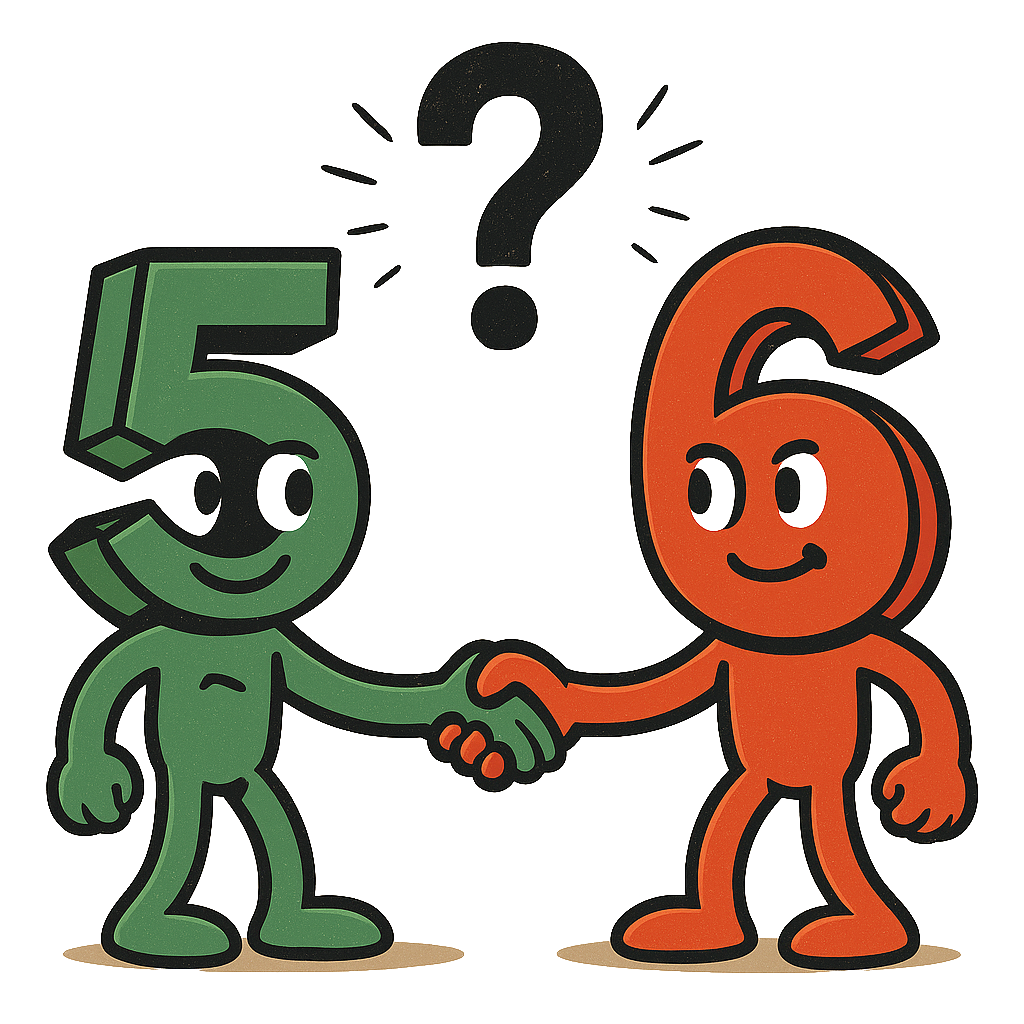
Was ist 6S - und woher kommt es?
Obwohl die 5S-Methode durch Toyota weltweit bekannt wurde, liegen ihre Ursprünge eigentlich bei Henry Ford. Bereits 1926 schrieb er in seinem Buch Heute und Morgen die sogenannte Modell CANDO:
C = Aufräumen
A = Arrangieren
N = Ordentlichkeit
D = Disziplin
O = Kontinuierliche Verbesserung
Es ist dem sehr ähnlich, was wir heute als 5S wissen. Toyota und später insbesondere Taiichi Ohno haben diese Prinzipien im Rahmen des Toyota-Produktionssystems (TPS) zu einer praktischen Arbeitsmethode weiterentwickelt. So wurde die berühmte japanische 5er-Variante geboren:
- Seiri (Trennung) - Entfernen Sie unnötige Dinge.
- Seiton (Arrangement) - allem einen festen Platz zu geben.
- Seiso (Reinigung) - Regelmäßig reinigen und kontrollieren. (Beim Ausrollen kehren wir 2 und 3 um)
- Seiketsu (Standardisieren) - Stellen Sie sicher, dass die ersten drei S strukturell gesichert sind.
- Shitsuke (Stehend) - Entwickeln Sie Disziplin und Eigenverantwortung, um dies beizubehalten.
In Japan begannen sie einst mit nur 4S. Der fünfte S, Shitsukeist ein selbstverständlicher Teil der japanischen (Arbeits-)Kultur. Wenn man sich dort auf etwas einigt, wird sich der Mitarbeiter daran halten. Im Westen mussten wir es explizit hinzufügen, weil Disziplin und kontinuierliche Verbesserung hier weniger selbstverständlich sind.
Einführung von 6S (5S + Sicherheit)
In der westlichen Welt ist eine Sechstes S hinzugefügt: Die Sicherheit. Damit wird die 5S-Methode zur "6S-Methode". Es klingt logisch: Sicherheit ist wichtig - also geben Sie ihr einen Platz in der Methode. Methodisch ändert sich wenig, denn in einem guten 5S-Ansatz ist die Sicherheit die gesamte Struktur tief verwurzelt. Bedenken Sie:
- Unter Sortieren (Seiri) Gegenstände entfernen, die eine Stolper- oder Brandgefahr darstellen.
- Unter Systematisieren (Seiton) verhindert das Herumliegen von Werkzeugen und verringert so die Verletzungsgefahr.
- Säuberung (Seiso) hilft, Lecks oder Verschleiß rechtzeitig zu erkennen.
- Standardisierung (Seiketsu) macht Sicherheitskontrollen zur Routine.
- Und mit Standhalten (Shitsuke) die Menschen aufmerksam und engagiert zu halten - auch in unsicheren Situationen (als Teil der regelmäßigen 5er-Runden).
- SicherheitGewährleistung einer sicheren Arbeitsumgebung durch Identifizierung und Management von Risiken während der ersten 5S- und
Mit anderen Worten: Sicherheit ist Teil des 5S-Konzepts. Das sechste S (6S) ist dann eine logische Folge, ein grundlegendes Ergebnis einer guten 5S-Politik.
5S und 6S: gleiche Methode und Absicht
5S und 6S mögen auf den ersten Blick unterschiedlich erscheinen, aber sie haben letztlich die gleichen Schritte und Ziele: einen sicheren, strukturierten und effizienten Arbeitsplatz. Das sechste S ist ein Wert, der vollständig mit der Lean-Philosophie übereinstimmt.
Aber wo 6S die Sicherheit explizit nennt, sorgt 5S dafür, dass die Sicherheit implizit mit jedem S entsteht, wenn man die Methode sorgfältig und mit Disziplin. Sicherheit ist dann kein zusätzlicher Schritt, sondern eine unmittelbare Folge einer intelligenten Organisation.
Wir stellen daher die Sicherheit in den Mittelpunkt des 5er-Kreises, weil jeder Schritt dazu beiträgt.
Was leistet sie?
- A sicherer Arbeitsplatz
- Engagierte Mitarbeiter
- Einfachheit: Standardteil Ihrer Arbeit
- Nachhaltige Sicherung
- Mit anderen Worten: diejenigen, die 5S / 6S ernst nehmen, baut die Sicherheit an der Quelle auf. Das macht sie nicht nur effektiver, sondern auch viel nachhaltiger.
Schlussfolgerung
Wer auf Sicherheit bedacht ist, muss nicht gleich ein sechstes S hinzufügen, er kann es aber natürlich. Vor allem müssen Sie die 5S-Schritte richtig ausführen, dann wird sich die Sicherheit daraus ergeben. Mit engagierten Teams, klaren Standards und kontinuierlicher Instandhaltung des Arbeitsplatzes entsteht auf natürliche Weise eine sichere Arbeitsumgebung. Das ist die Essenz von Lean - und die Kraft von 5S und 6S.
6S, Unterschied 5S und 6S, Lean 5S, Sicherheit am Arbeitsplatz, 5S Sicherheit, Toyota 5S, Lean Sicherheit, Lean Management