The big turnaround at Bluekens: how 5S changed the workplace and the team
At Bluekens Truck and Bus, the mobility of their customers is their number 1 priority. In a transport and mobility industry that continues 24/7, where customer satisfaction, safety and efficiency are of crucial importance, standing still is not an option. When the parent company Volvo Trucks, the Lean for Retail program, Bluekens seized the opportunity to further professionalize their processes.
Within that program, Bronze is the first level. This includes a focus on 5S, daily starts and KPIs. Volvo wants each dealership to designate at least one location this year to start this process. Progress is monitored via a Lean for Retail audit. For Bluekens Truck and Bus, that was Breda, because this is also their largest location.
The result? A workshop that is impressive: tightly organised. They save six minutes per work order and the mechanics work more pleasantly and efficiently.
“You only know what you're missing when you see what it could be,” says Pjotr van Gils, business supportemployee at Bluekens Truck and Bus.
Why 5S at Bluekens Truck and Bus in Breda?
The workplace in Breda is the largest location. With more than 30 mechanics, all with their own routines and preferences, tools and materials quickly became scattered. In addition, safety was an important point of attention. With grease pits, heavy vehicles and tools, a small mistake could have major consequences. And in a time when the workload is increasing and mechanics are scarce, you have to spend every minute wisely. That is exactly what Bluekens Truck and Bus has achieved with our guidance.
“A mechanic wants to tinker, not search for a battery charger or torque wrench. Yet that happened more often than we would have liked.”
The preparation: support as a foundation
Bluekens knew: a successful 5S implementation starts with support. That is why an integral approach was deliberately chosen. Every employee, from apprentice to workplace manager, was involved. No top-down story, but working together on improvement. Every mechanic received an A3 drawing of the workplace and was asked to design the ideal layout themselves. As Pjotr puts it so beautifully: “This made it their workplace, not an imposed image. It also gave us smart insights from practice.”
The challenge was not in motivation, but in the logistical preparation for the temporary closure of the workshop. In an environment where everything always continues, this requires tight planning and clear communication. Nevertheless, Bluekens decided to close the Breda branch for two days for the large-scale 5S redesign. Unplanned repairs continued as usual and we asked our customers to use one of our other branches during these days to ensure continuity. In this way, there was maximum focus.
The 5S rollout: creating space together
Pjotr looks back on the rollout: in the spring, the workshop was closed for two days. Together with 5S-Company, all mechanics got to work with the five steps of 5S: separate, clean, arrange, standardize and maintain. Some items had been lying unused for years. Saying goodbye literally created space.
"Where initially there was scepticism ("do we really have to shut down for two days for this?"), the atmosphere quickly turned into enthusiasm. Mechanics who normally worked individually, consulted and helped each other. The team spirit grew visibly. You saw people making choices together and improving together. That was really nice to see."
Embedding: 5S as a permanent habit
At Bluekens Truck and Bus, 5S has now been embedded in the daily work culture. With the help of the 5S-app and the Safety-app (including safety cross) the teams start each morning with a short day start in which actions, points for improvement and safety come together.
According to Pjotr, the app has really become a central point. Everything you need to know is in there. That keeps things moving. Daily starts, weekly checks, monthly internal audits and periodic checks by 5S Company ensure that the attention for 5S remains lively. “Notifications and actions are actively followed up, so that improvements are not diluted. By making successes visible, the support base grows. That is ultimately the key to really making 5S part of daily work,” says Pjotr.
Measurable and tangible results
The impact of 5S was immediately visible and tangible at Bluekens:
- Average of six minutes less search time per work order
- A safer workplace thanks to fixed locations and clear walking routes
- More job satisfaction through overview and structure
- A more professional appearance towards customers and visitors
- Easier to secure thanks to the 5S app and Safety app
Pjotr says: “We used to search for materials regularly. Now we know exactly where everything should be. That gives us peace and focus.” Collaboration on the work floor also got a boost. Discussions about lost items or unclear agreements disappeared, and job satisfaction increased noticeably.
And the icing on the cake was the official Lean for Retail audit by Volvo. The verdict was crystal clear: “We hardly have any comments or remarks, you are just doing very well,” according to the Volvo auditors.
It gave the Bluekens employees exactly what you hope for after such a 5S process: recognition, pride and, above all, a good dose of energy to continue building.
“5S is a powerful tool. The process at Bluekens perfectly illustrates how important it is in daily work: it helps in every area to work smarter, safer and more pleasantly. If you don’t know 5S, you feel that something is missing – but where exactly it pinches in the workplace remains unclear. That which you are missing is 5S. And once you know it and use it, you don’t want to be without it. Just like your trusted cordless impact wrench or ratchet set,” according to Dennis van de Bunt, owner and Lean/5S consultant at 5S-Company.
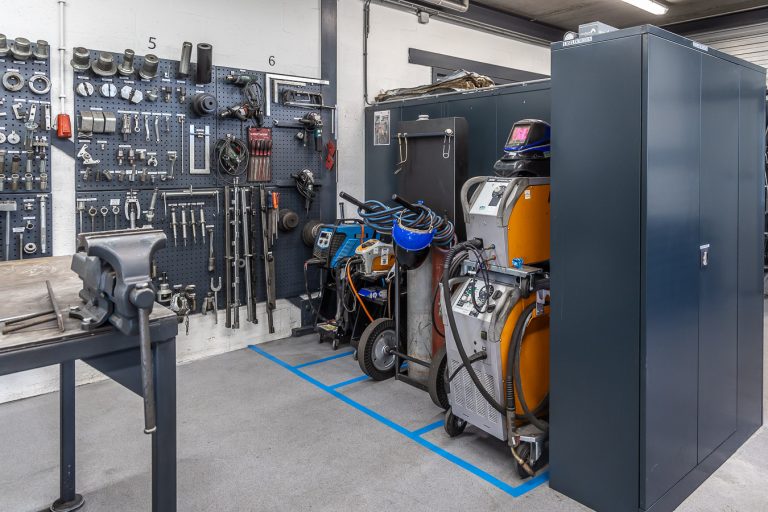
"Practical, flexible and committed" – this is how 5S-Company helped Bluekens move forward
Pjotr van Gils says that 5S-Company played an important role in the rollout. The external guidance brought structure, speed and depth. After all, a fresh pair of eyes is a bit compelling, and their practical approach fitted in perfectly with the way Bluekens likes to work. From the start, 5S-Company actively participated, both in the preparation and during the implementation. What do we need? What should we pay attention to? This approach ensured that the process not only ran quickly, but also smoothly. Their support was also valuable in the embedding. They helped to set up the process as effectively as possible: with daily starts, the 'looked at the week' structure, frequent coaching, the use of the 5S app and external audits, the focus on improvement remains continuously present.
Ready for the next step(s)
“We see 5S as a hard reset: a new start with more structure, better cooperation and room for growth. After the successful implementation in Breda, we are now rolling out 5S to our other branches. Middelharnis is next. In order to get started with registering and following up on small actions, we are activating the app directly at all other branches.
My tip for companies that are hesitant to start with 5S? Just do it. Don't just look at the numbers, but especially at the people. Employee satisfaction is becoming increasingly important, and 5S can really give it a huge boost. We believed that beforehand, but now that we have experienced it ourselves, we are 100% convinced - even though some colleagues thought differently at first 😉," says Pjotr.
We are grateful for the trust that Bluekens Truck and Bus has placed in us and proud that we can contribute to their growth. We wish the entire team much success with the further rollout of 5S within the organization and will of course remain involved in the next steps.
Meet Bluekens Truck and Bus
At Bluekens Truck and Bus they work together on progress, so that their customers drive and keep driving. Bluekens Truck and Bus is an official dealer of Volvo Trucks, Volvo Bus, Renault Trucks and Renault Trucks commercial vehicles. In addition, they are the trusted partner for many public transport companies and coach companies. Their branches can be found in Breda, Roosendaal, Oosterhout, Goes and Middelharnis. With over 200 colleagues, they put the mobility of their customers first.
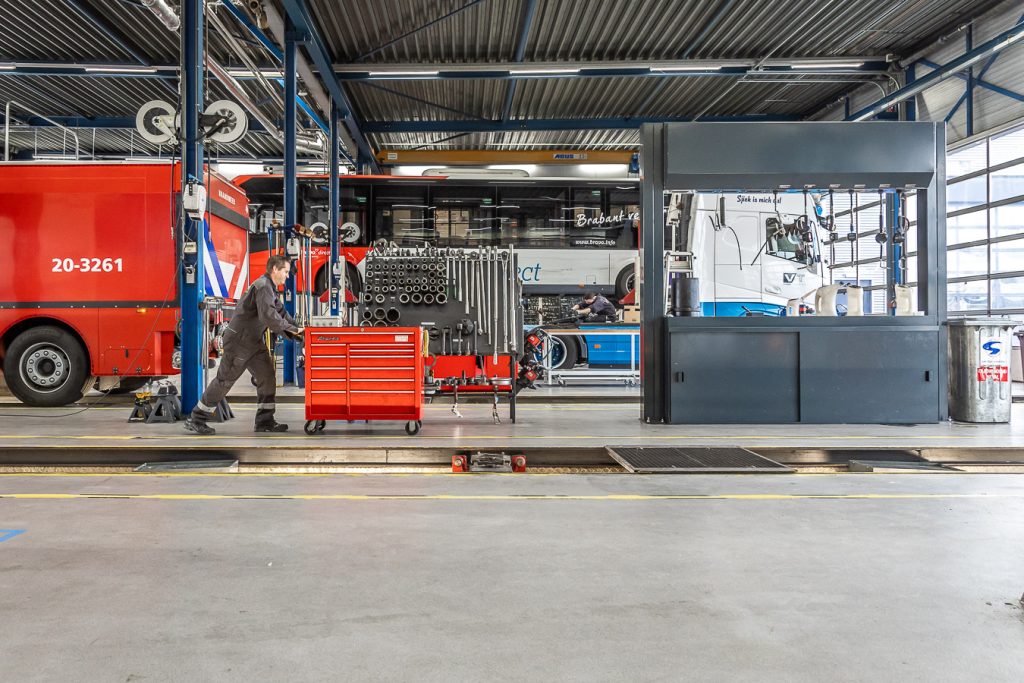