5S success at Thermo King Transport Refrigeration: From Pilot in Venlo to national 5S rollout
Thermo King Transportkoeling, specialist in refrigeration machines for road transport, strives for service excellence in its nine Dutch branches. After a successful 5S pilot in Venlo, the company has proudly rolled out the process nationally. Jim Versteegen, Regional Manager South Netherlands with 13 years of experience at Thermo King Transport Koeling, shares why 5S is crucial, how the implementation went and his personal experiences with this transformation. Discover how 5S became a game-changer for Thermo King Transport Refrigeration.
Why 5S at Thermo King Transportkoeling?
Thermo King Transportkoeling, with nine service locations in the Netherlands, places a high priority on safety and efficiency. Jim Versteegen, Regional Manager South Netherlands explains: “Our parent company sets high standards for safety, and we knew there was a lot to improve. Although we were already busy tidying up and cleaning, we sometimes became blind to the daily things. The goal was clear: “Transform all our locations into workplaces that function perfectly and (continue to) look neat”.
“We started the pilot in Venlo, in one of our larger locations. During the rollout, we asked workshop leaders from other locations to help. This way, it was a win-win situation, because they received that help back in the approach of their own location. It was very valuable to involve other workshop employees in the 5S roll-out in Venlo. This resulted in mutual understanding and experience with 5S in action. After the successful guidance by 5S-Company in Venlo, it was our task to roll this out independently across all locations in the Netherlands.”
The implementation phase at Thermo King Transportkoeling
Under the leadership of Marcel and Dennis (from 5S-Company), we started the 5S process with dedication and expertise. We provided a detailed plan, including diagrams and preparatory assignments such as the spaghetti diagram, to clearly map and improve the walking routes of mechanics. “This helped us identify faster and especially shorter routes. In the meantime, we also looked at items that are hardly or no longer used. People tend to keep too much under the motto: It might come in handy someday. During the major 5S rollout, we were closed for two days, while mechanics from another location kept the breakdown service running. Together with 5S-Company, we emptied the entire workshop, set up a red label zone (to use items for which there was still doubt whether they should actually be thrown away) and cleaned thoroughly, from the floor to the ceiling lighting and everything in between. This is the time-consuming part of 5S.”
5S-Company, together with Thermo King Transportkoeling, reviewed the plans and drawings of the employees who use the workshop most of the day and analyzed the data. This helped to determine where materials could best be placed or repositioned. “We put everything on an A0 drawing to make it easier to discuss in groups. For example, based on the spaghetti diagram, we discovered that the nuts, bolts and screws were in a corner of the workshop, which caused unnecessary walking movements. We asked our supplier to divide the workshop into three stations and also with less stock. This resulted in less movement and simplified work processes.”
“5S-Company is a very nice company to work with”
“The tight schedule of 5S-Company was an eye-opener for us. Their enthusiasm and realistic approach were exactly what we needed. They tell it like it is, which is not always easy to hear, but is crucial for us. Something that often takes a lot of effort is to get people excited about change. I really admire how 5S-Company does this: they motivate everyone from the start and make sure we work according to the 5S rules.”
“Will things work out okay this way?”
“Marcel (from 5S-Company) warned us that we had to stick to a tight schedule and that was right. It took some getting used to at first, but already on day two we saw that everything fell into place: from timing to work distribution and reorganization. Despite our initial doubts, the approach of 5S-Company proved its worth. They kept us sharp and ensured that we continued to think critically.
Before we started the 5S rollout for the other branches ourselves, we 5S-app, boards and tablets from 5S-Company installed in all our branches. These (hardware and software) tools were essential to successfully activate and embed 5S in each location. The penny dropped for our employees as soon as they saw the (partly by themselves) transformed workplace. By continuously motivating them and integrating the 5S process into their routine, they keep the workplace itself in top shape. Problems are solved automatically by the overview that the 5S board offered. With the 5S app and tablets, employees regularly take photos, give comments and keep an eye on the workplace.
Now the 5S day start and the 5S board an integral part of our daily work. The periodic audits of 5S-Company, led by Marcel, give us a fresh look from outside and help us stay on track. Michiel (former colleague) and I have now also implemented this success to all branches of Thermo King Transportkoeling, which took about half a year. The help of colleagues from other branches was self-evident, because everyone saw the benefits.”
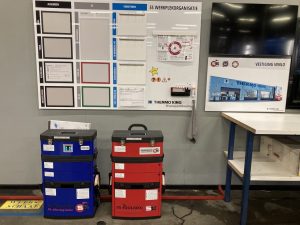
“I've never seen the workshop like this”
That is the best compliment we can receive from customers, because with us the customer is king! This confirms time and again for workshop managers and mechanics that we are on the right track. Customers and drivers share their positive experiences with their managers and directors, which ultimately strengthens our reputation and cooperation.
A major improvement through 5S is our inventory management. “We have cleaned up the attics and warehouses with non-moving parts, which not only optimizes the physical space, but also has a mental relief. A tidy workplace also means a tidy mind,” says Jim. This has led to more efficient management of our inventory and a more organized workplace.
The improved walking routes are another significant result. Jim notes, “Although improving walking routes seems simple, it has had a huge impact on our efficiency on the shop floor.” These changes have helped us save time and speed up processes.
In addition, 5S has strengthened collaboration between branches. “Regular communication has improved collaboration and strengthened the working atmosphere,” says Jim. This leads to a more cohesive, effective organization where branches are no longer seen as separate entities. The 5S process and 5S Company have definitely helped us to make Thermo King Transportkoeling more future-proof, which is something every company strives for.
Jim's golden tip: “Plan a visit to a company that has already completed a successful 5S trajectory”
Michiel (former colleague) already had a connection with 5S-Company. “We visited Bakker Bedrijfswagens, which had gone through the same process with 5S-Company. Their enthusiastic experiences gave us an extra boost and confirmed our positive expectations. It was inspiring to see how well it went there. If you have doubts about a 5S process, plan a visit to a company that has already successfully implemented it, such as Bakker Bedrijfswagens or now with us. This will give you a clear insight into the results and benefits. I am 100% convinced that after such a practical visit you will not only see the added value, but also want to start with 5S right away.”
Meet Thermo King Transportkoeling
Thermo King Transportkoeling is a leading specialist in road transport refrigeration equipment, offering efficient and reliable cold chain solutions. With high-quality cooling technologies from Thermo King and Frigoblock, and the expertise of Thermo King Europe and Trane Technologies, they optimize the conditioned fleets of its customers in, among other things: national international, pharma, retail and intermodal transport. They ensure that goods are transported at the correct temperature, in compliance with strict environmental, noise and food safety requirements. With 9 service locations in the Netherlands and a global network of certified technicians, they offer reliable support and service.