Home » 5S Implementation » Gemba walk
GEMBA WALK: a walk around the workplace
Identify and track problems on the shop floor, improve processes, increase employee engagement and ensure greater safety during daily processes. The Gemba walk provides a clear picture of what is really happening in the workplace. The purpose of Gemba is to identify disruptions and challenges in the workplace that you want to improve.
- Detecting problems in the workplace
- Increasing security
- Strengthen trust and commitment
- Clear understanding of what is happening in the workplace
- Understanding the potential for improvement
- Good input for preparing a 5S implementation
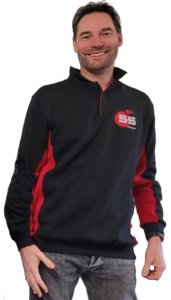
Increase knowledge of practice with Gemba
To roll out 5S effectively, knowledge of the practice is necessary. Gemba is an initial introduction and analysis of the workplace. Freely translated, it means Gemba walk "round on the workplace". It looks at the various processes, tools and even walking directions on the shop floor. On this page you can read what the purpose of a Gemba for 5S and what this round looks like. We will also give you practical tips and explain the different steps of this comprehensive and insightful workplace analysis.
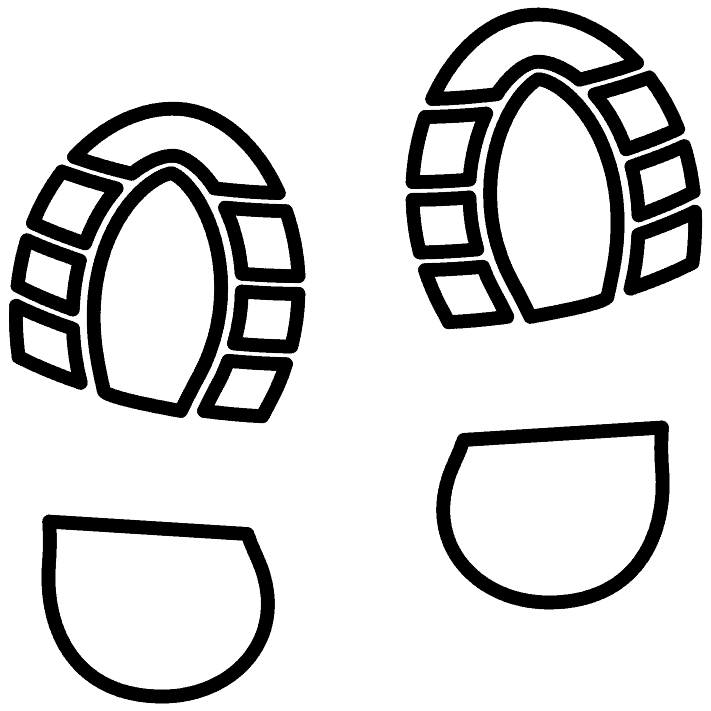
GOAL OF A GEMBA WALK
The purpose of the Gemba walk is actually seeing on the workplace what the processes and wastes are. The 5S method has a set structure, but no shop floor is the same. Many times, employees are used to the work environment and overlook the waste and potential. The Gemba provides a fresh and sharp look at improvement potential, and this information is used to determine what is needed for an effective 5S rollout.
Employees are also interviewed to find out about familiarity with 5S, what the 5S level of your organization is and to what extent one can apply it. Basic knowledge of 5S is included in the theory portion of the 5S rollout. If additional knowledge and application of 5S appears desirable or necessary, there is 5S training. This training increases the knowledge of everyone in the organization with 5S.
During the 5S rollout, all the S's from the 5S model are put into practice. These are the steps of the execution phase of the 5S implementation on your workplace.
Assess the 5S level of the shop floor with a 5S audit and verify that 5S has been effectively applied within the organization. Or request a 5S audit to determine the 5S level on your workplace.
5S training is designed to familiarize everyone in a company with the 5S method. Work on effectively implementing 5S within your organization and become a star at 5S!
Gemba and 5S into practice: the roadmap
Together with an in-house employee, 5S Company conducts the 'round on the shop floor’. All processes are looked at separately and per process one or more employees are interviewed. Points that need to be considered during the gemba walk:
- Unsafe situations
- Extinguishing agents not available
- Emergency exits blocked
- Acting unsafely
- Lack of proper personal protective equipment (PPE)
- Use of rejected tools
- Failure to comply with safety requirements
- Inefficiency
- Unnecessary movements
- Too much or too little stock
- Waiting
- Overproduction
- Walking routes
- Bypassed by inefficient layout
- Obstacles
- Workplace layout
- Logical classification by material use
- Storage of materials
- Logical place for use
- Correct quantity
- Correct conditions
- Wastes
All findings are collected and contribute to an effective 5S roll-out according to the 5S method.
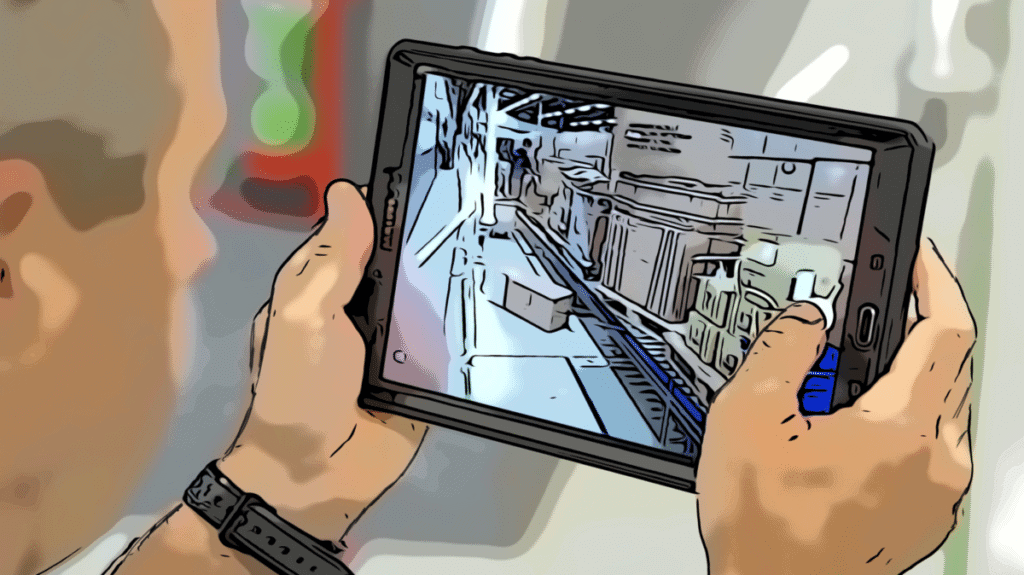
What is Gemba?
Gemba is a well-known concept within the Lean philosophy. In Japanese, that word literally means "the real place. Within 5S, it means "the place where it happens": the workplace. The concept of the Gemba walk was developed by Taiichi Ohno. The round lets managers, executives and employees see firsthand how work is done by visiting and analyzing the workplace.
The concept has three main elements:
1. Go and have a look
Visit the workplace and see if processes are being carried out correctly. Do not rely only on what is written on paper or what employees tell you, but see with your own eyes how work is performed and record problems or disruptions.
2. Ask why
Ask employees and other stakeholders questions to better understand processes and discover why things are done a certain way. Based on the answers and observations, this knowledge provides room for coming up with new ideas for process optimization.
3. Show respect
Understand challenges employees face by engaging with people. Decide how to address and approach them without compromising safety, quality and productivity. Respect employees' time, do not disturb them while they are working and show appreciation for their efforts.
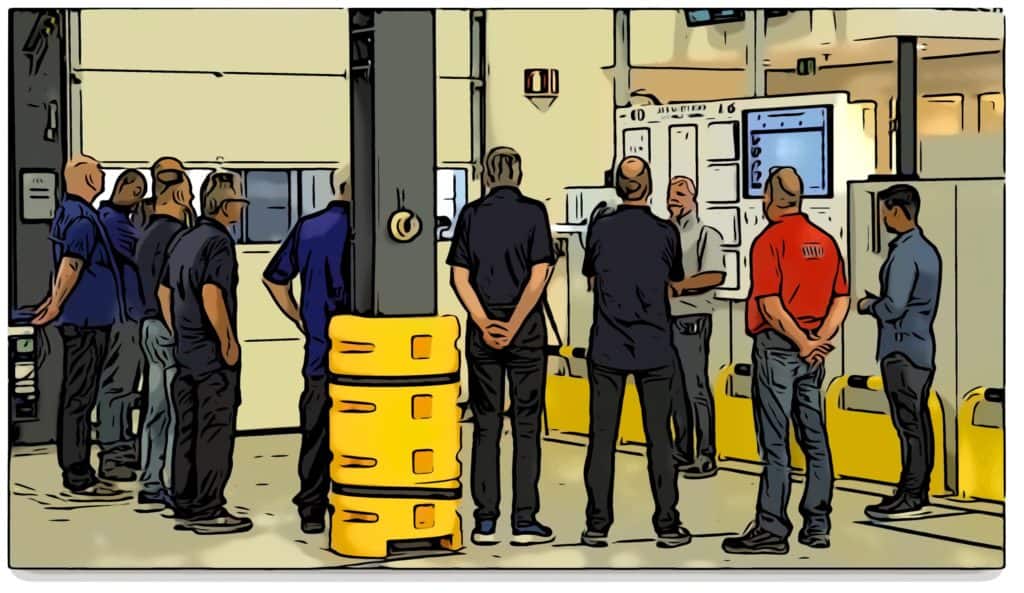
Improve and optimize processes with 5S Company
Because of 5S Company's extensive experience with 5S implementations on many different shop floors, we quickly see where the waste and potential for optimizations and improvements are. 5S Company offers a fresh and critical look at your processes, the layout of the shop floor and finds out the root causes. We translate the findings into the 5S rollout, giving you a tight, safe and efficient shop floor.
5S can be applied to any workplace, within any industry. Find out how 5S Company helps you work more safely, efficiently and profitably. A successful 5S implementation in three phases.
Get more insight and control over the results of your 5S deployment with the 5S App. The application supports you in securing 5S on the shop floor and easily conducting 5S audits.
Sort, shine, set in order, standardize and sustain. These are the 5 S's of the 5S Method. Read all about the benefits and application of the 5S Method, 5S Company's specialty.