Kaizen at Scalabor: optimizing work processes for human development
Erwin Lenderink, one of the team leaders at Scalabor with a Greenbelt in Lean, is responsible for the mechanical packaging, assembly, logistics and personnel departments. With years of experience in this industry, he takes us on the 5S journey and the continuous improvement process. Curious about the driving force behind 'kaizen' at Scalabor? Then read on and discover how our strong collaboration, perseverance and support have made these steps possible.
Why 5S and CI trajectory at Scalabor?
Scalabor carries out various activities, including packaging, shrinking, making bicycle pumps, machine work and warehouse work. “More than 4 years ago we started implementing the 5S method via 5S-Company in one department to optimize their work processes. This start went with some fits and starts and functioned reasonably well, but the approach always seemed to be watered down. Many work supervisors felt that 5S work was considered an additional burden rather than an integrated part of their duties.
However, at the beginning of 2022 we made a new start with 5S-Company. With more emphasis from the management team and the principle of “forcing strangers' eyes”. This enabled us to conduct an in-depth analysis of the work supervisors' tasks. We asked ourselves: Where is our focus? And what are we responsible for? This analysis revealed a striking insight: we were spending too little time on our core business, namely people development. There was little structure in our work processes. Methods, instructions and results were not properly secured, which led to excessive crowding.
While we viewed people development as our core mission, we discovered that in practice we invested little in this task. An in-depth study we conducted over 6 weeks revealed that only 5% of our employees' time was spent on development, while most of the time was spent preparing orders and receiving goods. In response to this insight, we identified two Kaizen projects to address this issue.
Purpose of Scalabor
The ultimate goal? A well-organized company, or in other words, running an efficient and streamlined production company. Take, for example, packing a Christmas package with 10 items. Imagine: while packing we notice that there are only 8 of those items. What now? We say: STOP! Instead, we should ask: When will we receive the missing items? Do we proceed with the package or wait? It is much better to assess in advance whether everything is there to start. We used to just leave everything there, with no room for anything else, and the warehouse would become overcrowded. Now we understand that this was not a good approach. We have now become smaller and have made clear, achievable agreements, both with customers and with business agencies, about how we organize this,” says Erwin.
The biggest challenges: acceptance and change at Scalabor
The most challenging task is gaining acceptance across the organization at Scalabor. Reaching consensus to implement and secure lasting improvements. “It was not an easy task, as we now see in our Kaizen conversations between warehouse, production and business office. These changes also required a different approach towards our customers.
Previously, our warehouse did not always check what was delivered, and we often had unclear information about incoming freight. This led to unpredictability in staff deployment. We started as a company that did everything to satisfy our customers. In social employment, we adapted to every customer wish, without asking questions. For example, if a pallet fell apart due to incorrect placement on a truck, everyone simply cleaned it up and started again. However, we forgot to ask: what went wrong? Was the fault with the supplier? This shift from a customer-centric approach to self-decision was a challenge. And sometimes it is still difficult to fully implement this.”
Self-awareness in Scalabor's work culture
At the moment, Scalabor is at a point that has not been reached before, but it is clear that everyone involved is happy with this. That really stands out. The people currently involved ask each other questions that arise from the principles of 5S/Lean, something that managers strongly encourage. Employees know that their manager questions them about a specific topic every week, so they cannot sit still. They will dig into it, and that is exactly what happens at Scalabor. They know questions are being asked. For example, if a delivery comes in and there is not enough material, the first question is: “What does the packing slip say?” These are things that people are going to apply, and if that packing slip isn't there, the question becomes, "Why didn't anyone report this?" The expedition has the task of reporting this so that the business office can contact the supplier or customer. This growing degree of self-awareness is evident at Scalabor.
“We encountered some challenges during the move, but we are now correcting each other. People recognize the matter. In the beginning we noticed that employees saw it as something extra, something that came "on the side". “I prefer to do it after half past four,” you often heard back then. But now people are increasingly starting to realize that it is just part of their daily work. That is a positive development. Work planners bear responsibility, but increasingly delegate tasks to their assistants. In short: the stricter approach is paying off,” says Erwin.
The future of Scalabor
“We are now looking ahead to the Kaizen group being dissolved and replaced by a Lean assurance group to ensure these improvements are sustainable and implemented across the organization. Our good cooperation, perseverance and support have brought them to these steps. Our plan is clear: we are going to reduce dependency on specific people. We strive to no longer work without instructions. It is not acceptable to start with the idea of “I know, I don't need instructions.” Our goal is that everyone can function smoothly, regardless of who is present. That is what we want to achieve with this process.
What I initially expected was that many people thought this would be a 1 to 1.5 year project. But now we've been working on it for 2 years, and last year I told everyone: “I won't see the full implementation before I retire.” My hope is that everything will be properly secured and documented by then, but fully integrating these methods will take more time.
MEET SCALABOR
Scalabor is the social development company for Central Gelderland. They help people who need support in gaining and maintaining a place in the labor market. Anyone who can work, but cannot make it on the labor market without support. Including people with an occupational disability, social assistance or Wajong. At Scalabor their possibilities and talents are developed and connected to work. With the aim of active participation in society. For employers, Scalabor offers well-developed personnel and supports efficient and sustainable business operations, resulting in a win-win situation for both employees and employers.
Website Scalabor
Value Stream Map
The Value Stream Map is crucial for establishing standard procedures so that everyone can work in the same consistent way. “Sometimes you have to interview people to understand how they do things. It's not about control, it's about understanding. If you do it well, you can be an example for others. At first people didn't really understand this, but when I told them what I had captured, they realized it was exactly what they were doing. “That really makes me excited,” says Erwin. This has helped us determine whether customers can meet our requirements when delivering goods to our expedition/warehouse.
“Scalabor is clearly on the move, and we can learn a lot from similar organizations such as Gazelle, which are constantly striving for improvement. It is important to realize that implementing 5S and Lean is not a short journey, especially for companies with different turnovers like us. It is a process that requires broad support, and I am convinced that external expertise and 'outside eyes' play an essential role in its success. This will lead to further spread of positive changes within our organization, as we can already observe.”
We are grateful for the trust that Scalabor has placed in us. Would you like to stay informed about the further steps we are taking in our journey towards continuous improvement? Then keep a close eye on us!
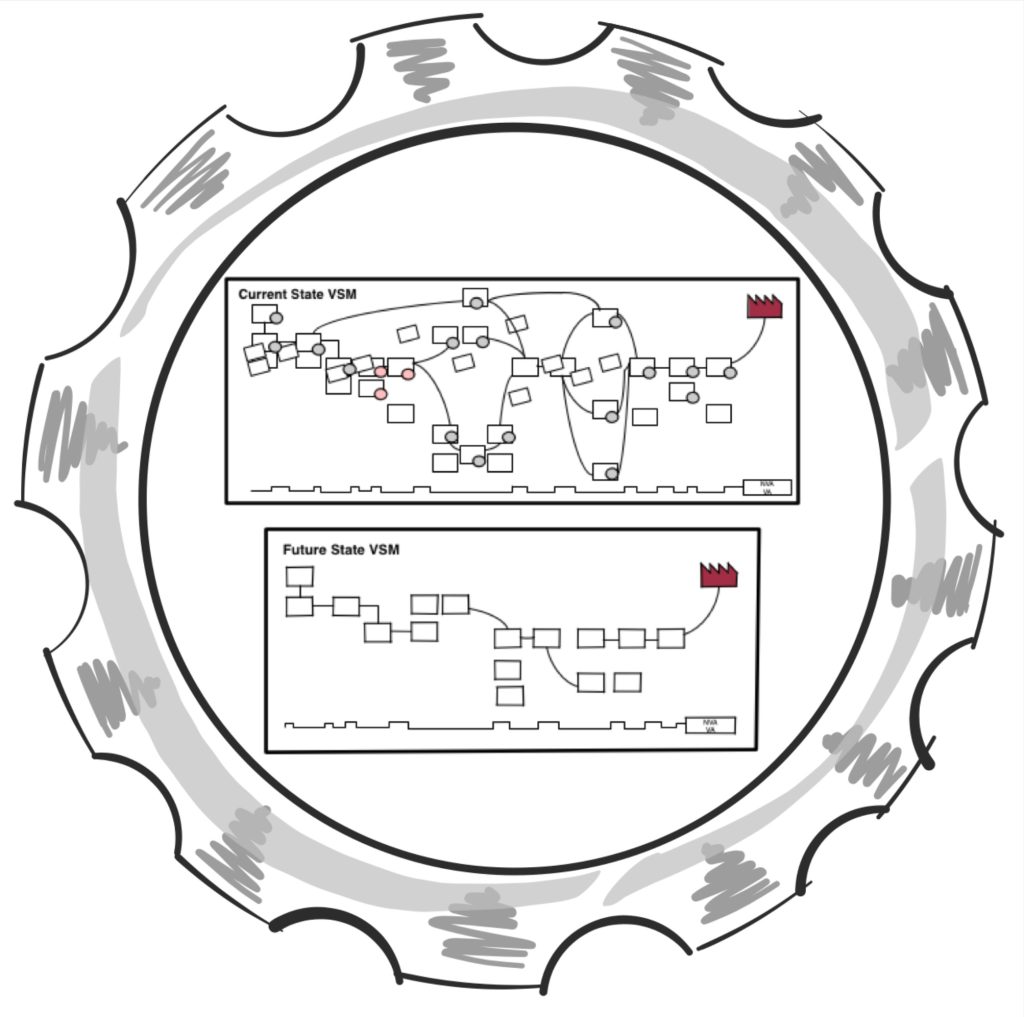
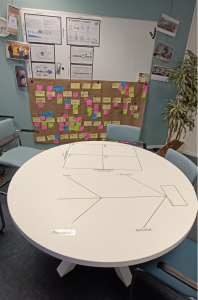
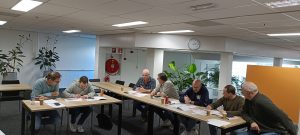
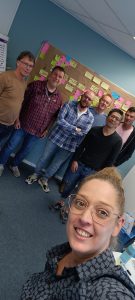