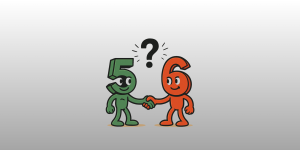
5S en 6s: overeenkomsten en verschil
Wat is het verschil tussen 5S en 6S? Overweeg je 5S of 6S
Home » 5S Methode » 5S-voordelen
Bereken hier de kosten van zoektijd binnen uw organisatie.
Krijg inzicht in de kosten van onnodige stops van bijvoorbeeld een productie lijn.
Bereken hier de kosten van schades en vergelijk deze met de kosten van een 5S implementatie.
Liever samen analyseren hoeveel 5S binnen uw organisatie kan opleveren?
De 5S-methode helpt bedrijven veiliger en efficiënter werken. Deze bewezen methode voor werkplekorganisatie wordt wereldwijd gezien als de standaard van de ideale en meest efficiënte werkomgeving. Het toepassen van 5S binnen uw organisatie levert diverse voordelen op.
Op deze pagina beantwoorden wij de belangrijkste vraag: wat levert 5S op? Dit doen we aan de hand van een uiteenzetting van 5S-activiteiten die u kunt toepassen binnen uw organisatie. Daarnaast hebben we verschillende rekenmodellen en Return-On-Investment-voorbeelden voor u opgesteld.
√ Een veilige werkomgeving
√ Minder verspillingen
√ Efficiënter en effectiever werken
√ Een opgeruimde, nette werkplek
√ Meer werknemersgeluk
√ Hogere winstgevendheid
Bovenaan de lijst met voordelen van 5S staat uiteraard veiligheid en daarmee het voorkomen van ongevallen op de werkvloer. Daarnaast draagt de 5S-methode dagelijks bij aan het terugdringen en verminderen van verspillingen. Dit levert automatisch een voordeel op dat bijdraagt aan effectief en efficiënt werken. Hoewel het soms lastig kan zijn om deze besparingen en optimalisaties exact vast te stellen, bieden wij u hieronder een (onvolledig!) overzicht op welke vlakken 5S uw organisatie versterkt.
• Blusmiddelen zijn goed bereikbaar
• Nooduitgangen niet geblokkeerd
• Medewerkers met de juiste persoonlijke beschermingsmiddelen (PBM’s)
• Gebruik van goedgekeurde gereedschappen
• Navolging van veiligheidseisen
• Efficiënte indeling en looproutes zorgen voor minder onnodige afstanden
• Voorraad afstemmen op vraag en aanbod
• Minder wachttijd producten en werknemers
• Geen overproductie door visueel (pull) mechanisme
• Logische (ergonomische) werkplekindeling, minder onnodige bewegingen
• Flexibele werkplek indeling, inclusief toelevering materiaal (fit for purpose)
• Inzicht in voorraden en ouderdom
• Logische plek voor gebruik
• Juiste hoeveelheid van materialen
Bij een goede 5S-implementatie stijgt de arbeidsproductiviteit. Een onderdeel dat zeker in deze tijd voor veel bedrijven van groot belang is. De uitdagingen op de arbeidsmarkt maken het lastig om nieuwe medewerkers te vinden. De 5S-methode zorgt ervoor dat u méér uit uw mensen haalt.
Bent u benieuwd wat 5S voor uw bedrijf kan opleveren? 5S Company verricht graag een nulmeting voor uw bedrijf om de potentiële opbrengst en optimalisatiescore van het implementeren van 5S binnen uw organisatie te bepalen. Deze nulmeting kan ook plaatsvinden in combinatie met het 5S Activatiepakket van 5S Company. Dit 5S-starterspakket is een laagdrempelige, betaalbare kennismaking met 5S voor uw bedrijf, waarmee u een 5S-pilot start op één geselecteerde afdeling.
Hieronder hebben we een aantal praktijkvoorbeelden uitgewerkt van 5S-implementaties en de resultaten van deze 5S-uitrollen. Ook schetsen we een inzichtelijk beeld van de Return-on-Investment (ROI) voor het toepassen van 5S op een productielijn en binnen de onderhoudsafdeling.
Als we 5S uitvoeren realiseren we dat medewerkers minder hoeven te zoeken naar materialen en gereedschappen. We richten ook betere visuele controle punten in gedurende het proces. Hieronder hebben we een aantal ervaringsgetallen. Deze gelden uiteraard niet bij iedere organisatie, maar zijn eerder conservatief dan overdreven.
Dan is potentieel: 50 werknemers x 0,25 uur x 230 dagen x € 30/uur = € 86.200 arbeidskosten
Omdat het zoeken dagelijks terugkeert en veelal bij iedereen gebeurt, de een iets meer dan de ander, komt dit totaal op een grote kostenpost uit. Het nadelige effect van zoeken, los van deze arbeidskosten, is dat je productiviteit verliest.Je kunt als je aan het zoeken bent immers weinig andere werkzaamheden doen, soms zien we dat zal zelfs een productielijn hierdoor structureel later kan opstarten na een wissel (van ploeg of product). Verliezen van productie (omzet) kost uiteraard ook geld!
De kosten per product gaan hierdoor ook omhoog, aangezien je de totale som van kosten deelt door minder producten.
Deze improductiviteit zorgt ervoor dat als je toch de gewenste output wil behalen, je meer capaciteit moet inzetten (50 x 0,25 x 230 =2870 uur). Capaciteit is echter op dit moment erg schaars, daarnaast komen hier aanvullende overhead ballast en kosten bij van recruitment, onboarding, administatie etc.
In een goede 5S inrichting wordt er ook gebruik gemaakt van uitgebalanceerde min-max met als doel dat de materialen die nodig zijn in het proces tijdig aanwezig zijn. Inclusief een tijdig aanvulsignaal (=kanban) waarbij voldoende tijd (berekend) is om tijdig aan te vullen.
Als je er daarentegen pas achter komt dat iets er niet is tijdens produceren, dan kost het in de regel vaak toch wel enkele minuten totdat zaken zijn aangevuld. Bij een lopende band betekent dit vaak dat de totale band stil staat, dit kost niet alleen productie. Maar ook de kwaliteit gaat naar beneden, werknemers raken uit hun ritme, waardoor de kans op fouten groter wordt.
Stel de situatie is:
Dan is potentieel: 10 werknemers x 5 lijnen x 20 min per lijn/dag x 230 dagen x € 30/uur = € 115.000 arbeidskosten
Terugkerende benefits
In beide reële gevallen is er veel potentie om te verbeteren, laat 5S in de eerste fases 50 – 75% van deze verspilling reduceren, dat zijn jaarlijks terugkerende benefits. Daarnaast activeert 5S verdere verbetering om het basiswerk (los van het zoeken) efficiënter uit te voeren. Elk jaar een verbetering realiseren die dagelijks opnieuw 10 minuten oplevert per dag is bij elkaar een enorme efficiency slag. 5S is vaak een start voor verdere procesverbeteringen!
Wij kunnen op een eenvoudige manier analyseren en een indicatie geven van de aanwezige tijdverspilling is in uw processen. Hiermee kan dan redelijk snel een Return On Investment (ROI) berekening gemaakt worden.
Een calculatie voor schades kan helpen om de ROI van een 5S-implementatie inzichtelijk te maken. We hebben een simpele calculatietool die de kosten van schades inzichtelijk maakt en deze vergelijkt met de kosten en potentiële voordelen van een 5S-implementatie.
1. Aantal incidenten per jaar: Het aantal keer dat er schade ontstaat (bijvoorbeeld door botsingen, valpartijen, verkeerd gebruik van gereedschap, etc.).
2. Gemiddelde schade per incident (€): De gemiddelde kosten die ontstaan per incident.
3. Indirecte kostenfactor: Bijvoorbeeld een factor 1,5 of 2 om de indirecte kosten (zoals stilstand, onderzoek, of reparatietijd) mee te rekenen.
4. Potentiële reductie door 5S (%): Een schatting van hoeveel incidenten je kunt reduceren door 5S in te voeren (bijvoorbeeld 20-50%).
5S Company heeft een volledige 5S implementatie uitgevoerd bij een klant met productielijnen. De onderdelen op deze lijnen worden per batch gemaakt en geassembleerd. Iedere reeks heeft zijn eigen onderdelen en specials. 5S heeft grote bijdrage geleverd aan omsteltijd reductie of te wel SMED. Zorgen dat de juiste materialen compleet en op tijd beschikbaar zijn en dit visueel zichtbaar maken.
Tijdens de implementatie is er gekeken naar het voorkomen van de verspillingen, creëren van flow en meer pull gericht werken (bouwen op basis van klantverzoek in plaats van op voorraad bouwen). Medewerkers stonden minder te wachten, schakelde sneller tussen de batches (omsteltijden van de assemblage en bevoorrading) en hadden minder herstelwerkzaamheden. Door kortere omsteltijd kan er ook een kleinere batch-grootte worden gehanteerd.
De complexiteit van het product is gedurende laatste jaren extreem toegenomen door productinnovaties waar de markt om vraagt. Dit heeft het assemblage proces veel ingewikkelder gemaakt, daarnaast is het volume ook nog 20% toegenomen! Dit gebeurd echter met dezelfde aantal werknemers en in dezelfde ruimte . De productiviteit per werknemer is hierdoor 10% toegenomen.
Door aanpassingen aan de aanlevering en assemblage kan er voldaan worden aan complexere klantvragen
Door de werkvloer slimmer in te richten kunnen medewerkers efficiënter hun werkzaamheden verrichten
Door het creeren van flow en een first time right proces, is er 20% meer output gerealiseerd
Al deze veranderingen kosten 0% meer ruimte en levert op verschillende plekken op de werkvloer meer vrije ruimte op
Waar onderhoud voornamelijk een dienst is, is ook hier een berekening te maken in de benefits van 5S. Door het toepassen van een volwaardige 5S implementatie binnen de onderhoudsafdeling van een grote proces industrie fabriek, is het zoeken naar materiaal verminderd en de ‘hands on tool’ tijd gestegen. Hierdoor is er minder machine uitval met als gevolg een hogere beschikbaarheid van machines. Daarnaast hebben we 5S uitgevoerd met de operators, waardoor deze minder verspillingen hebben en meer output kunnen realiseren. Daarnaast hebben door beter visueel proces ervoor gezorgd dat er betere visuele ingangscontrole kan plaatsvinden, waardoor de kwaliteit van de grondstoffen die verwerkt worden aanzienlijk is verbeterd.
Dit alles resulteert in een betere OEE (Overall Equipment Effectiveness) en aanzienlijke betere financiële opbrengsten.
Duidelijk waar installatie deel en benodigd materiaal zich bevindt, en welk gereedschap benodigd is.
Door de werkvloer slimmer in te richten kunnen medewerkers efficiënter hun werkzaamheden verrichten
Hogere hands on tool tijd zorgt dat er meer werkbonnen afhandelt kunnen worden. Hogere OEE Overall Equipment Effectiveness (OEE)
Door betere visuele ingangscontole is de kwaliteit van de verwerkte grondstoffen sterk verbeterd
Wat is het verschil tussen 5S en 6S? Overweeg je 5S of 6S
De grote ommekeer bij Bluekens: hoe 5S de werkplaats én het team veranderden
Waarom lukt 5S niet? We worden regelmatig benaderd door bedrijven die vast zijn
Op de hoogte blijven van 5S-nieuws, actuele ontwikkelingen en innovatieve oplossingen voor een efficiënte, veilige werkplek en optimale werkplekorganisatie? Schrijf u nu in voor onze nieuwsbrief!